Gallery
We develop creative, comprehensive, and sustainable engineering solutions for a future where society can thrive.
Bringing Ideas to Life with Precision and Quality
Take a look at our gallery to see our machines and solutions in action. Here, you’ll find examples of the quality and results we deliver, showing how Soest Machinery helps bring your ideas to life.
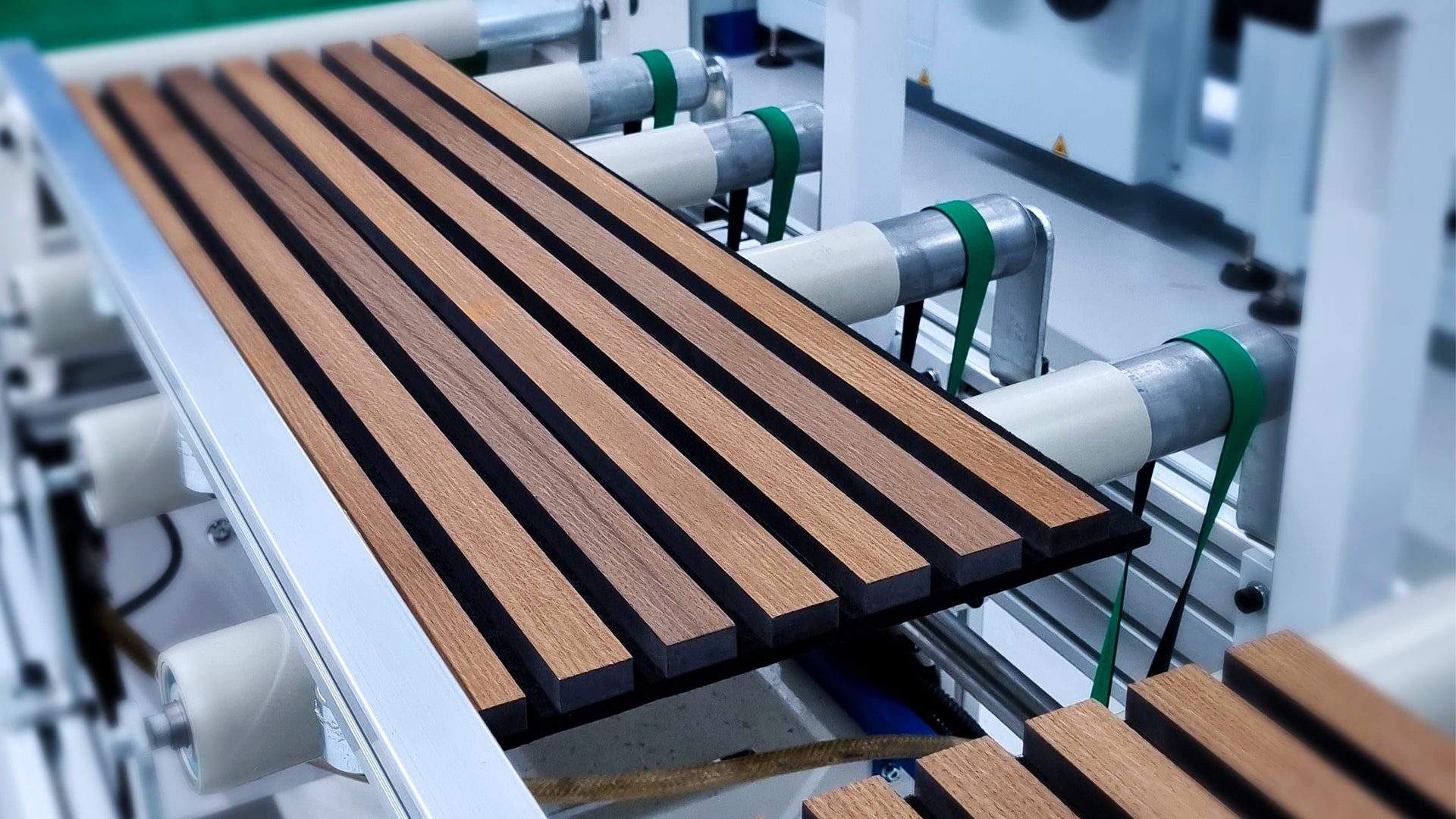
The process starts with placing the wooden slats into a specially designed holder. The slats pass through a glue roller that evenly applies adhesive to the back of each slat. At the indexing station, the felt backing is carefully positioned onto the glued slats, ensuring perfect alignment. The assembled panel then moves through a roller press, where consistent pressure secures a strong, even bond between the slats and the felt.
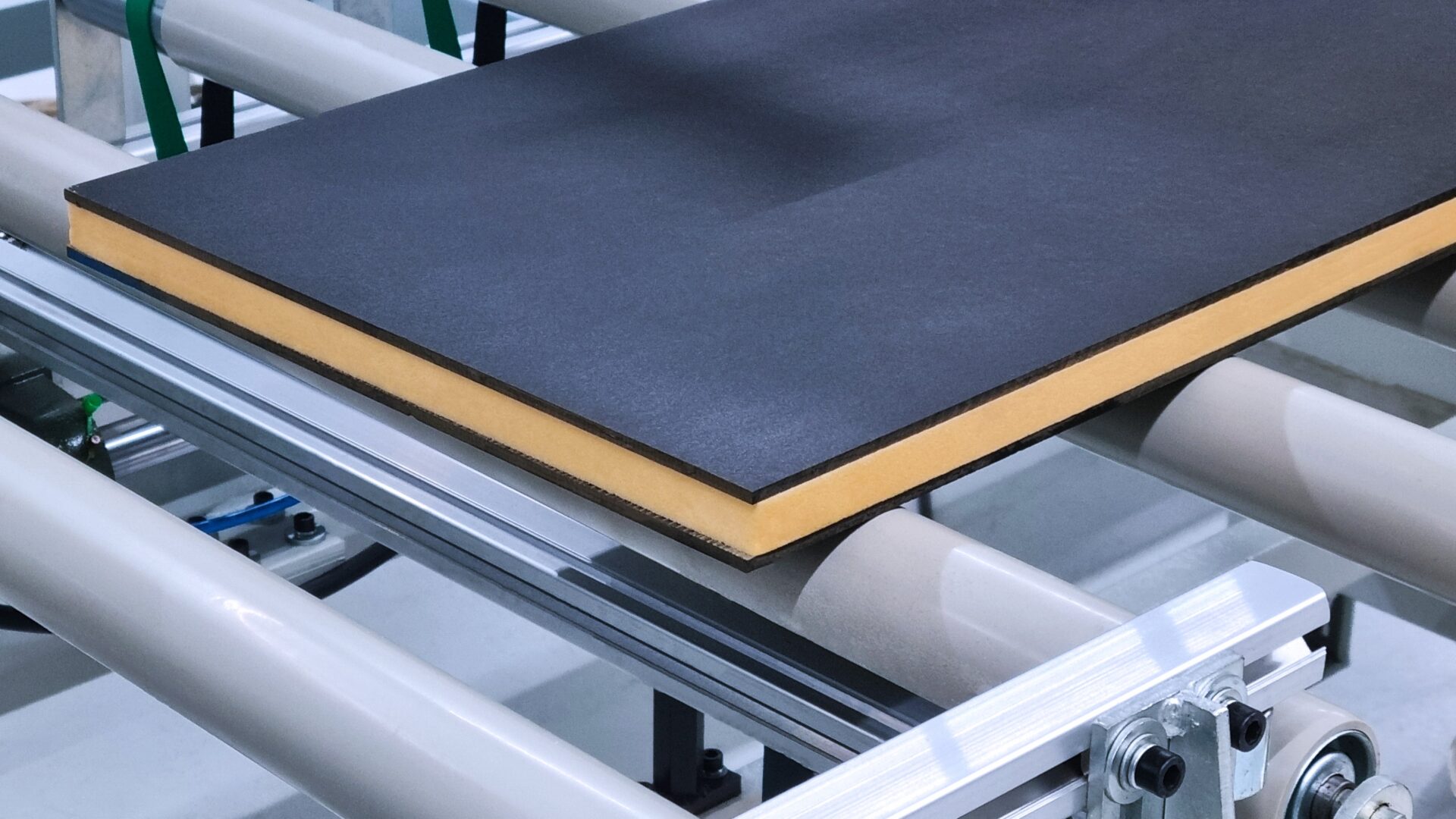
Our PUR-gluing line can be used for all kinds of products. Our wider lines can be used for the production or panels with insulation for example. Because the PUR-glue's strength is instantly at around 70% after pressing, you can work continuously, massively increasing your maximum output. The panels can be cut, moved, stacked or anything else, because they won't fall apart after pressing.
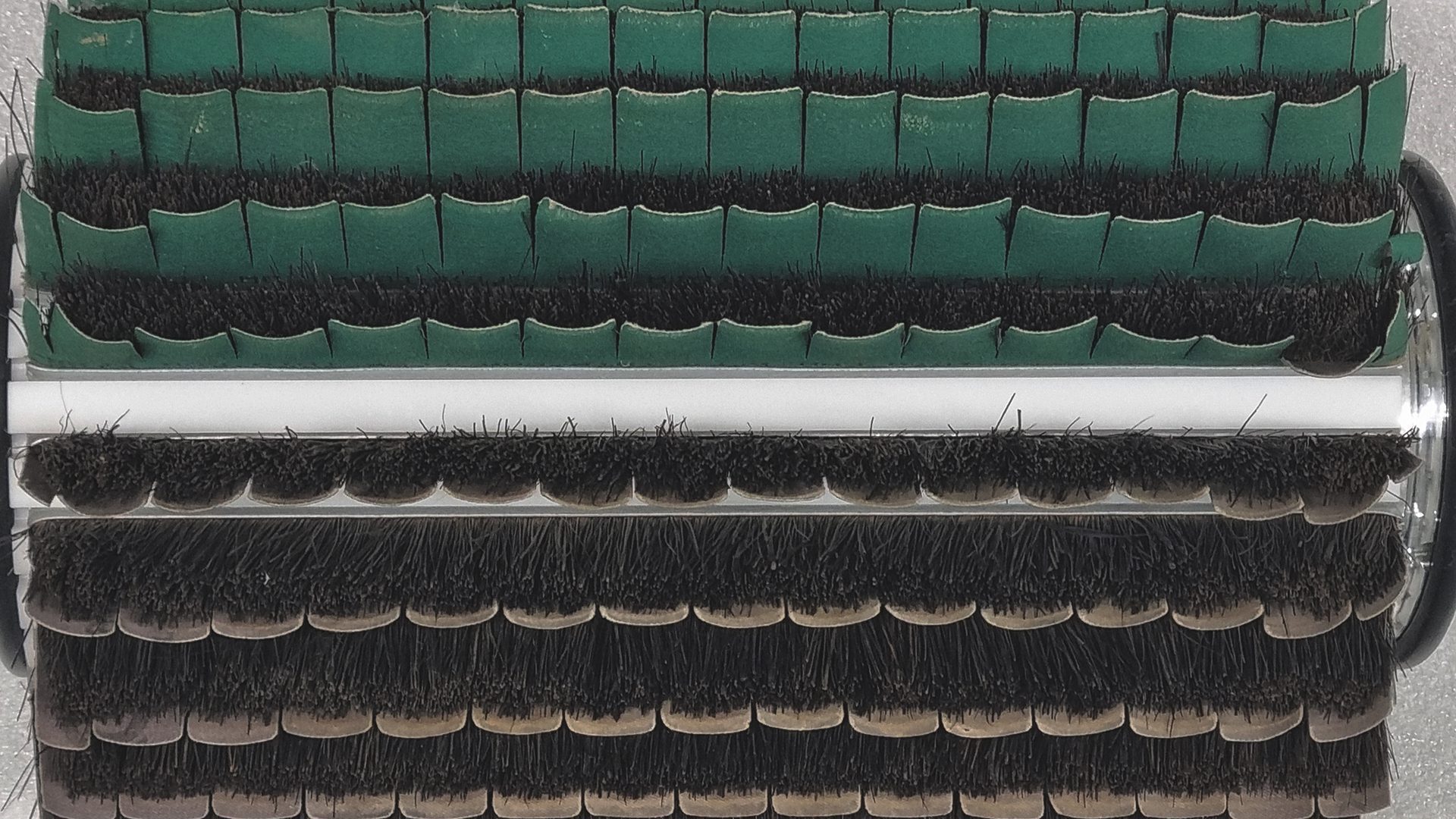
Denibbing is a crucial step in wood finishing that ensures a smooth, flawless surface. During sanding or between coats of finish, tiny fibers or dust particles—known as nibs—can rise to the surface, creating a rough texture. Denibbing removes these imperfections, enhancing the wood's appearance and preparing it for the next layer of finish. This simple yet essential process leads to a superior final product, highlighting the natural beauty and quality of the wood.
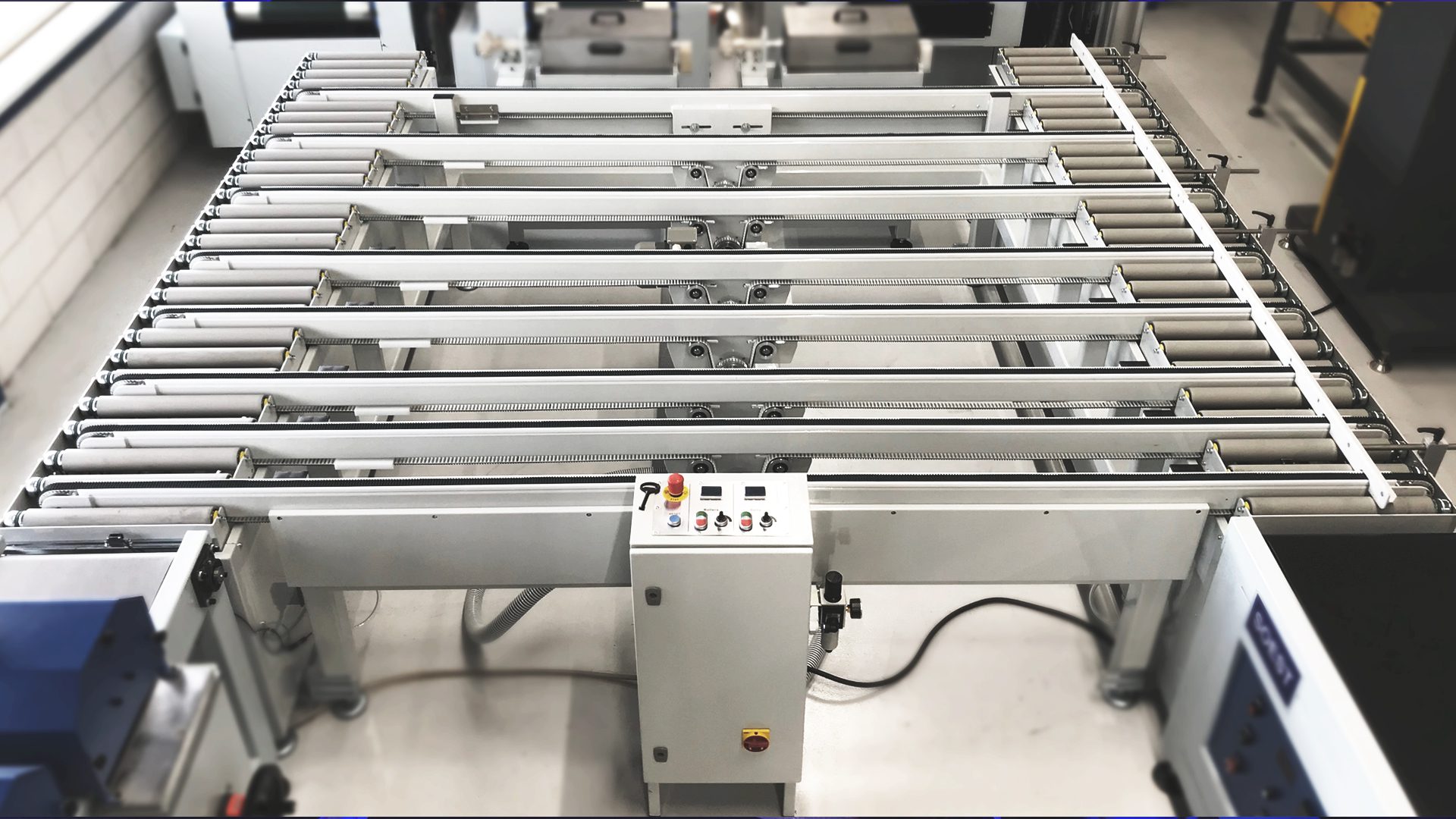
A transfer system is a great way to achieve the maximum efficiency if you're limited in length in your building. By using a transfer system, you can change direction of the product and the line, return a product to it's start, or allow for different types of production. By using a transfer system, you can keep everything moving at a steady pace, which not only speeds up production but also helps maintain consistent quality. We custom design the dimensions and speeds specific to your needs.
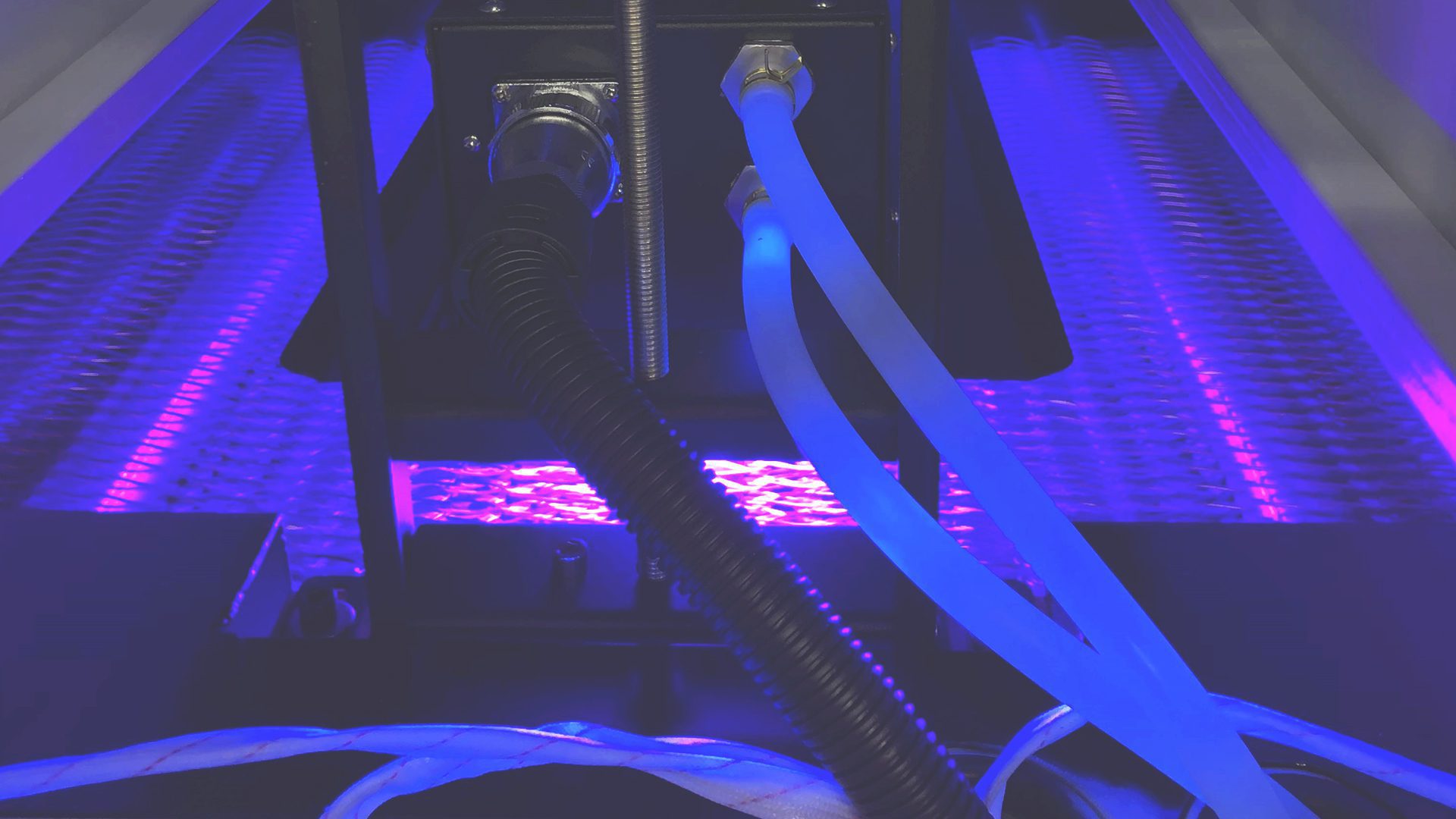
Drying tunnels using UV, LED, or infrared technology offer a faster and more consistent way to dry products compared to traditional air drying on racks. These systems dry products quickly and evenly, improving quality and reducing production time. Unlike air drying, which can be slow and uneven, drying tunnels help save space, cut down on labor, and increase efficiency. They’re a smart choice for businesses looking to streamline their production process while maintaining high-quality results.
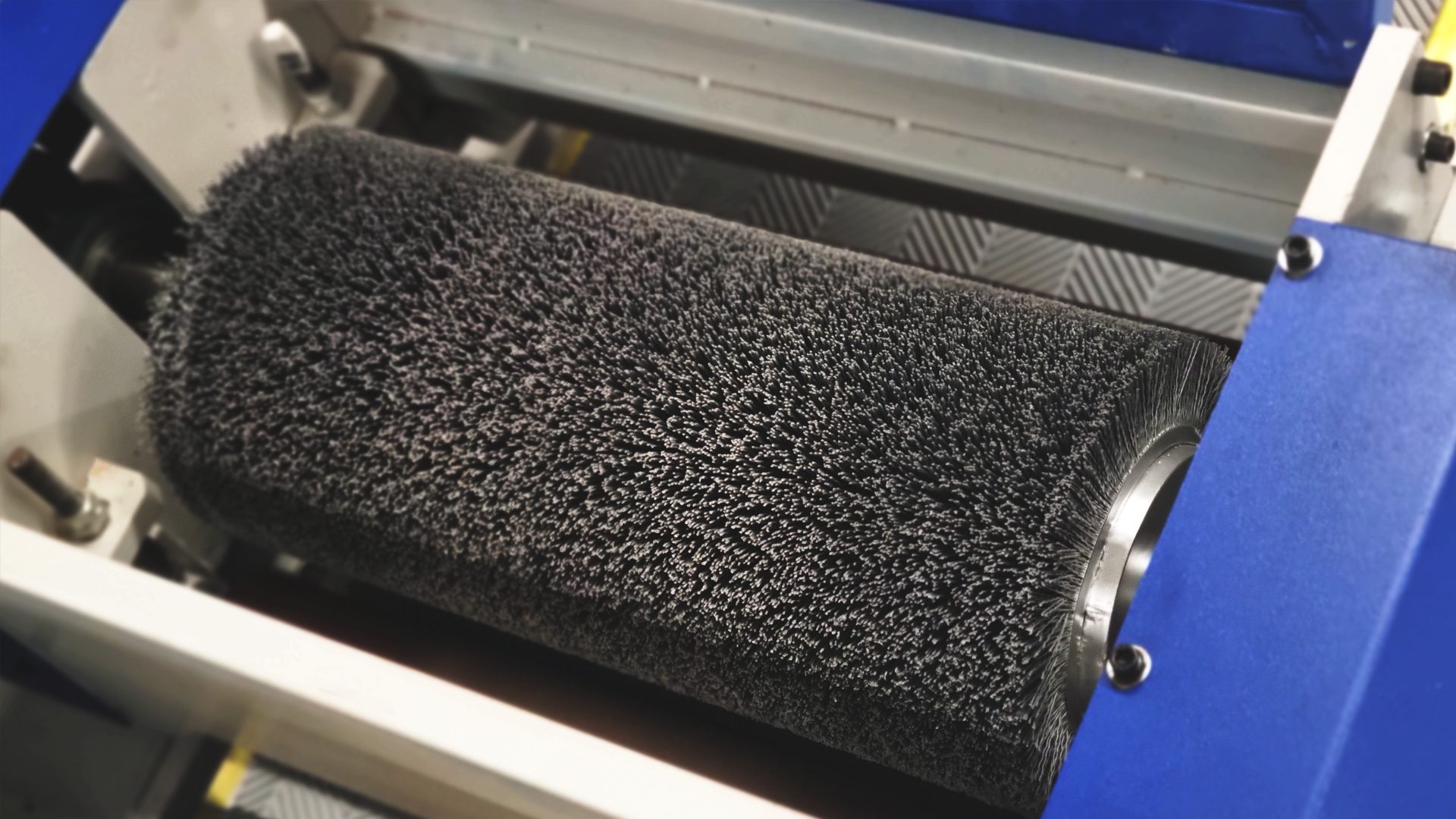
A structure brushing machine is a valuable tool for enhancing the appearance and texture of materials. It uses rotating brushes to create a uniform, textured surface, which can add a natural, aesthetic finish to products. Our machines have a wide variety of compatible brushes available, and can be customized to your production needs. Instead of manually brushing or sanding, a structure brushing machine provides consistent results every time, saving time and reducing labor.
What they say about us
Discover why our clients trust Soest Machinery.
But where the rubber meets the road is efficiently completing their objective. They meet their objective making everything easy. I have a roll coating machine line, Sand to dry. It sets inches from my shop wall, Every component, every adjustment and every wear/tear and cleaning screw is easily accessible. If you need to change a motor, which is unlikely, it’s a bit more intrusive because of where I placed them, but even then it’s not difficult.
Customer support…. I’m in USA they are in Netherlands. Despite the massive time difference, they are there. You could not complain.
I love my Soest machines and can’t wait to grow till I need more."

The tech support is very good Tools are made well and work great
Arjan has always been responsive and takes all questions seriously. Soest is a really solid company"
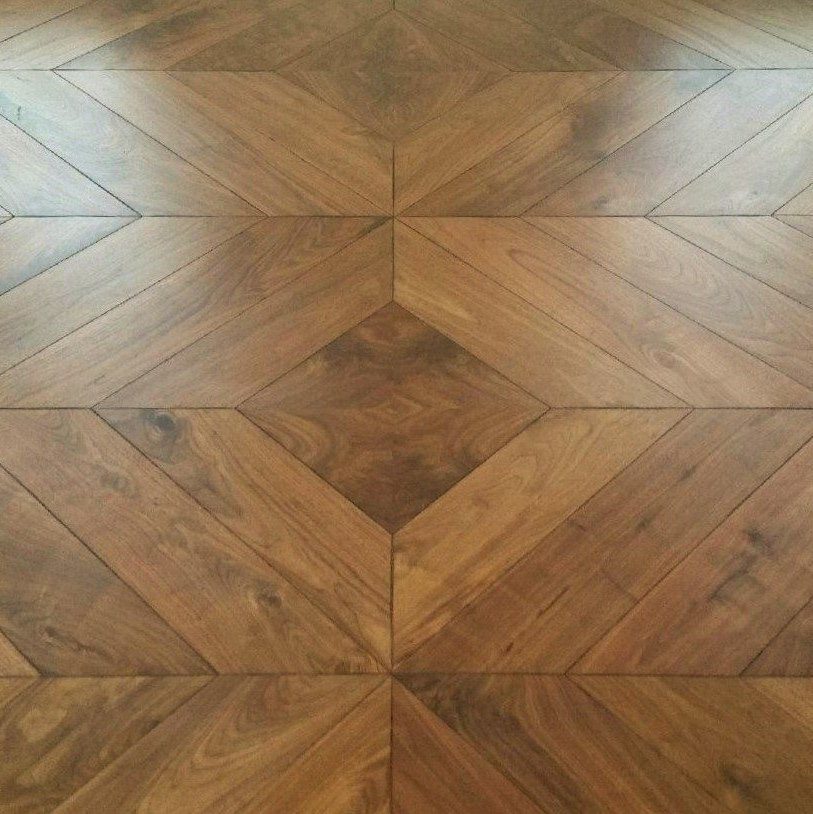
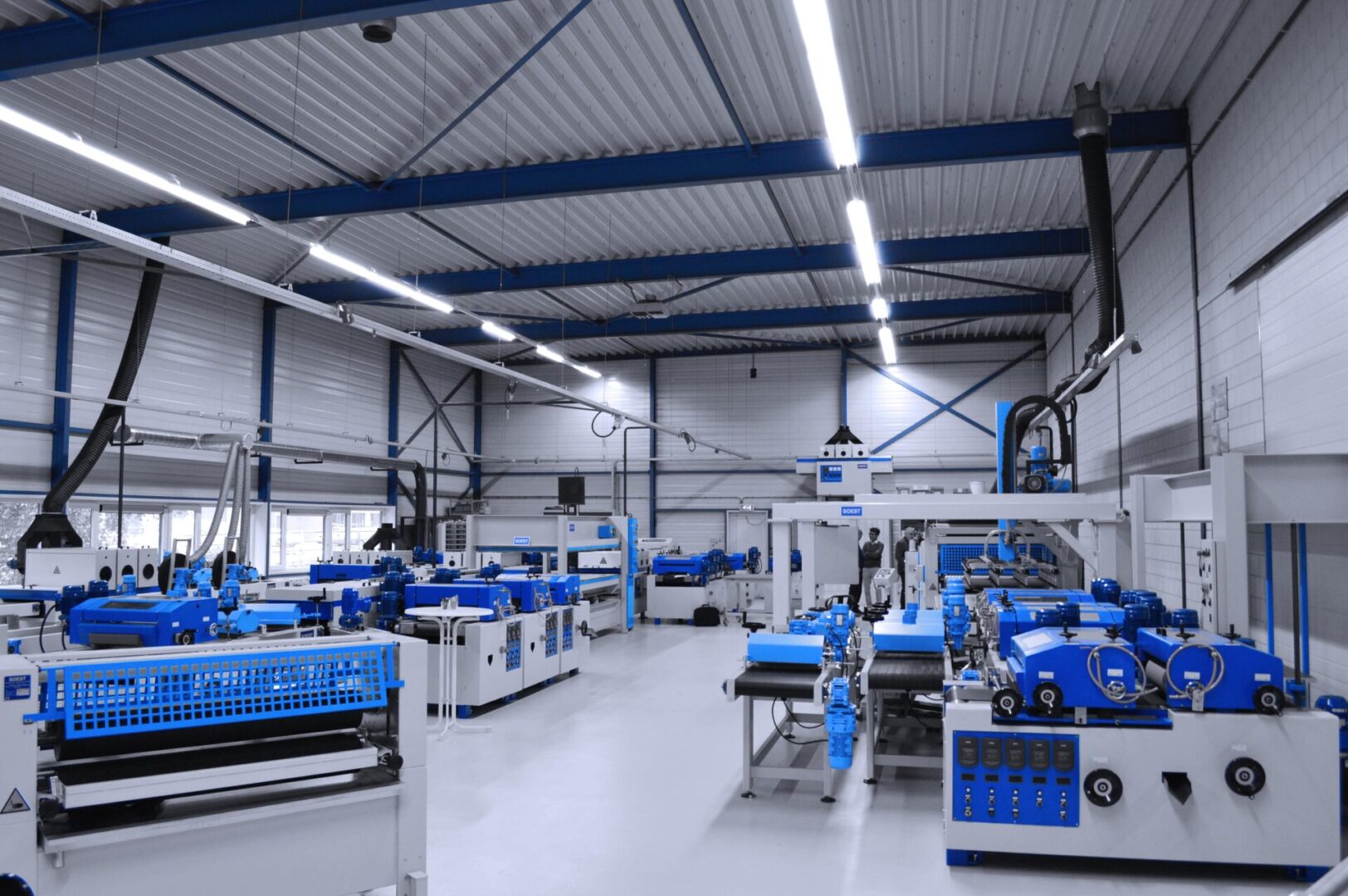
Get in touch with Soest Machinery today to discuss your specific needs. Our team of experts is here to help you select, customize, and optimize the right machinery for your business. Let’s work together to find the perfect fit for your operations!
Contact us now to get started.